Boliden Kokkola is a forerunner in industrial automation and digitalisation
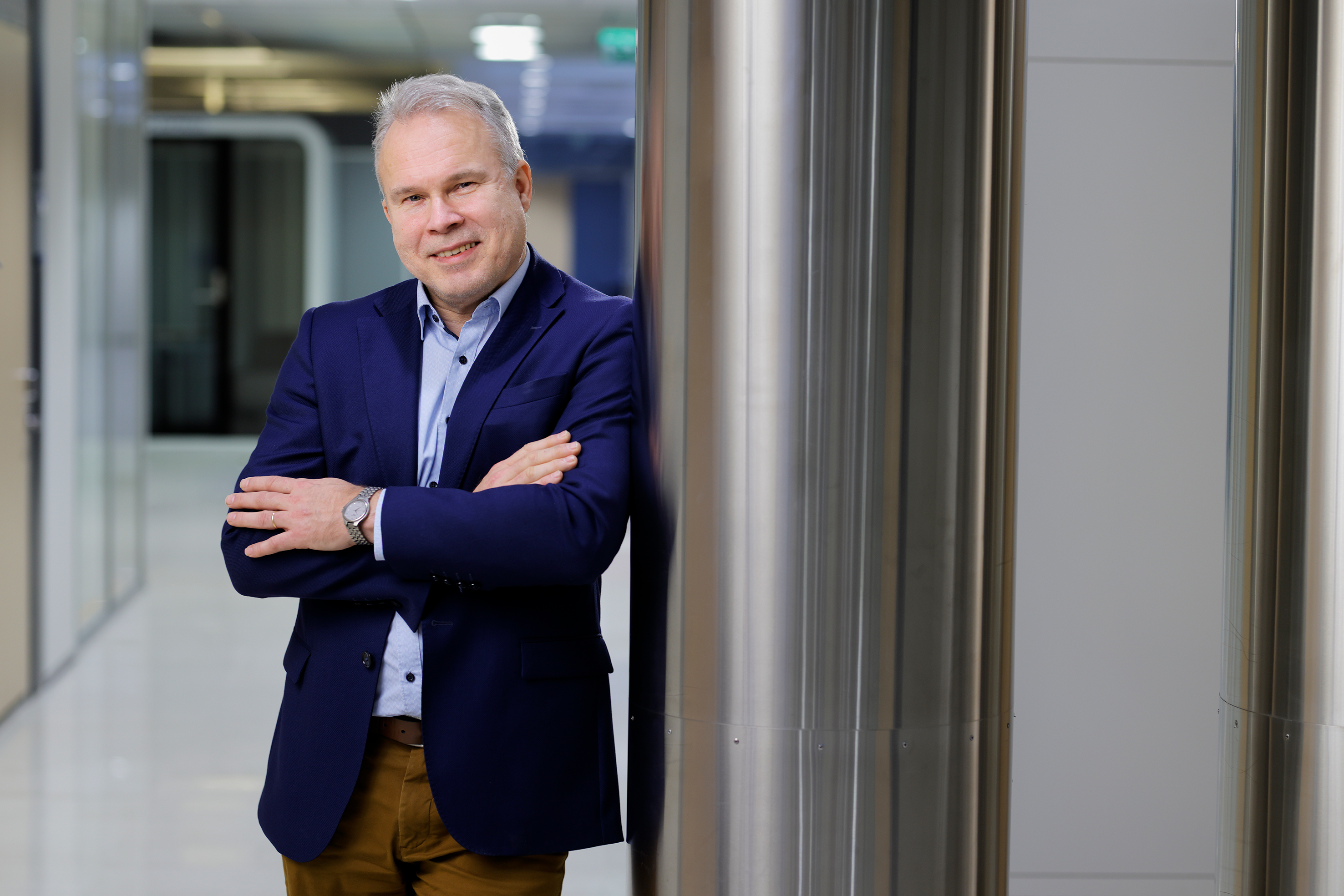
Digitalisation and automation have been hot topics in businesses around the world for many years now. Boliden Kokkola, one of the world’s biggest zinc smelters, is no exception. For a long time, digitalising and automating processes has been at the heart of Boliden Kokkola’s – and the whole Boliden Group’s – strategy.
“Our goal is to both increase efficiency and, most importantly, improve safety. When all routine and risky tasks are automated, people have more time to focus on safe tasks that require human skills”, says Antti Kontiainen, General Manager.
To achieve its automation goals, Boliden Kokkola has made many significant investments in new machinery – robots are now used in various tasks in the company’s zinc production. One of the newest automated solutions is an anode cleaning station.
“We have close to 40,000 anodes – lead-silver plates used in the production process – that need cleaning every month. On top of cleaning the anodes, the station uses machine vision to determine whether the anodes need maintenance and makes repairs when needed. Thanks to this investment, a lot of time is saved and our staff can fully focus on monitoring the process without dull work and safety risks”, Kontiainen explains.
The company has also decided to switch to automated forklifts in cathode transport. With their advanced navigation system, automated forklifts can move goods safely without a driver.
For Boliden Kokkola, investing in automation and digitalisation does not only mean new machines and vehicles, but also changes to data and knowledge management.
“By using applications that collect and visualize production data automatically, all our staff members have the same, realtime data at hand at all times. These modern reporting tools give us both reliable data about, for example, the production situation and a solid basis for decision making.”
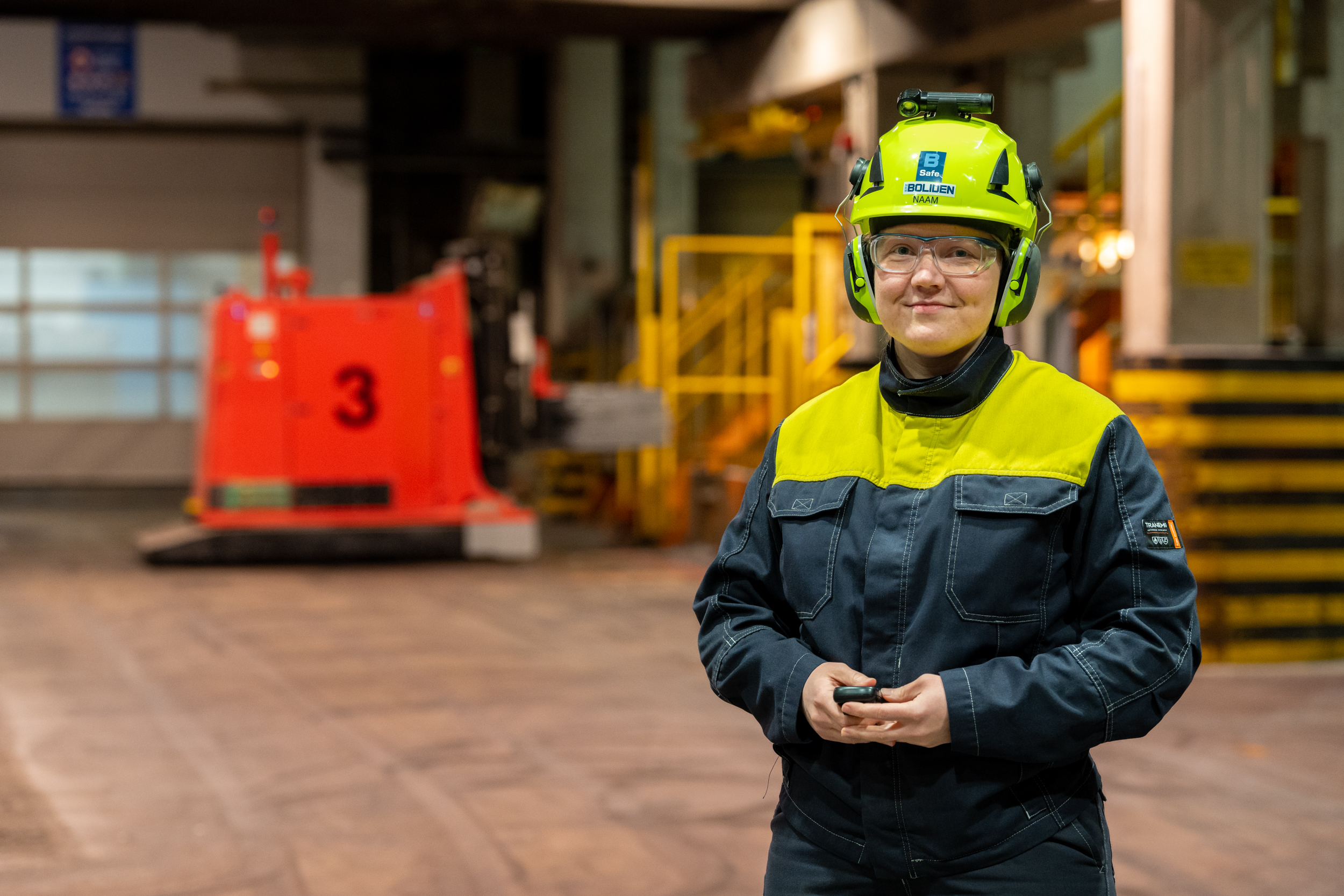